Today's guest blogger is Nick Stone, Mechanical Engineer, Z Corporation.
I design a lot of injection molded parts that have threaded inserts or receive self tapping screws. In order to prototype these parts for testing, I print them and install either brass inserts or HeliCoils. Here are some tips on how to use brass inserts and HeliCoils.
Brass Inserts
1. For the brass inserts (known as "threaded inserts for thermoplastics" on McMaster Carr) I drill a hole into the part the same diameter as the thickest part of the insert. You want a nice snug fit so the insert doesn't rotate, but you don't want to be hammering the insert into the part. McMaster-Carr shows a picture with a tapered section to the hole, but don't bother with that; a straight hole works just fine.
2. Thread the insert onto a 1/2" screw so the screw is about flush with the bottom of the insert for easy handling.
3. Coat the outside of the insert with Plastic Welder II. We've tried a few different epoxies and found this one to work the best in pretty much every situation. I'm also a huge fan of this stuff for gluing large parts together that I printed in multiple pieces. Get a bit of the epoxy onto the sides of the hole. Don't overdo it because you don't want to have any of the epoxy get into the insert threads.
4. Carefully push the insert into the hole and use a q-tip to clean off the excess epoxy that squeezes out.
5. If you're installing multiple inserts into the part make sure to have all of your inserts ready and threaded onto screws because the Plastic Welder will start to harden after about 5 minutes.
6. At that point you can carefully remove the screw making sure not to knock the insert out of alignment.
7. After about 20 minutes the Plastic Welder is firm and in 2 hours it's strong enough to install a fastener.
I used this method quite a bit to prototype the structural foam parts for the ZPrinter 650 which I printed on a Z810 in zp130 and infiltrated with ZMax. I've had great success with #8-32 and #10-32 screws. You can use as small as #6-32 but the surface area for glue contact is so little that I found these to be less reliable.
HeliCoil
Since we started using zp131 and zp150, I've moved to infiltrating with Zbond and using HeliCoils for inserts. As far as labor time and effort go, the HeliCoil is equivalent to the brass insert, but I think the final product is stronger and more accurate - plus, you don't have to wait for it to dry. The one downside to the Helicoils is that I haven't had any success trying to use thread locker on the fasteners.
For Helicoils, try to print the hole just slightly smaller than the required drill for the HeliCoil you plan to use. This insures that you'll get infiltrant deeper into the part than the threads will cut. If you have to drill away too much material, you might drill into the internal core of your part, and the coil won't hold as well. I prefer to dip my parts when I infiltrate, so it's a good idea to make sure to dab any excess Zbond that settles into the hole with a paper towel; it'll make drilling easier. The instructions for use are on the HeliCoil box but here they are anyway:
1. Drill out the hole using the recommended bit size.
2. Tap, being sure to go deeper than you need for the HeliCoil height.
3. Insert the HeliCoil and if desired break off the tang using the handy tool.
And that's it. The parts I've made using this technique see much smaller loads than when I used the brass inserts, however I've yet to twist one of these out. The most common mistake is not tapping deep enough, so be sure to do so. If the insert will be installed into a boss, make the boss wall thickness at least .090" in order to avoid having it crack during tapping. Thicker is better of course. With HeliCoils I've gone as small as #4-40 without any trouble.
Everything you need for either technique is available on McMaster-Carr.
http://www.zcorp.com/
skip to main |
skip to sidebar
Subscribe to:
Post Comments (Atom)
Search This Blog
Scott Harmon
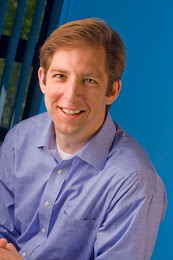
About Me
I am responsible for leading 3D Systems content creation and capture activities and, in partnership with business and functional leaders, developing new opportunities for the company. I have held a variety of leadership positions in marketing and business development and most recently ran a $150MM division of Church & Dwight, a leading consumer goods company. Prior to receiving my M.B.A from Harvard Business School, I was an Explosive Ordnance Disposal company commander for the U.S. Army. I graduated from the United States Military Academy at West Point with a B.S. in Electrical Engineering.
This is a common topic amongst customers. Thanks for the post. Has Z Corp tried melting threaded insert into a ZBuilder part?
ReplyDeleteGreat idea. I'll give it a shot and let you know.
ReplyDeleteGreat post, any update on what Andrew was saying Nick?
ReplyDeleteI know this was posted a while ago, so I understand if you don't get back to me. I have been getting my inserts from http://www.fasteningsolutionsuk.com/ - great affordable inserts.
It's good practice to install the HeliCoil so that the top of the insert
This short article posted only at the web site is truly good.www.3dprintinggeeks.com/
ReplyDeleteThanks...
ReplyDelete3d printed products
Thanks......
ReplyDelete3d prototyping